FS Construction
FS2V and FS3V chambers include a 304 Series stainless steel welded inner liner with high temperature fiberglass insulation. No asbestos is used in chamber construction.
The chamber outer case is fabricated from cold rolled steel finished in Bemco Blue. Chamber doors feature dual gaskets to fully vapor seal each compartment when the chamber is in operation. The internal transfer carriage is made from stainless steel. Four internal posts guide the cage and support optional test item fixturing, shelves, or baskets.
A double acting hydraulic piston and a built-in Bemco hydraulic power unit smoothly transfers the load basket(s) from chamber to chamber. To increase safety, the hydraulic piston is operated to its full stroke and is double acting so that transfers take place under full speed control. No cables or cable tensioning systems subject to wear and potentially dangerous failure are used.
The transfer system includes a positive mechanical transfer carriage lock, transfer carriage position indicators, limit switches in the hydraulic piston, and a time delay sensor set to sense transfer failure.
The electrical control panel is hinged for easy access.
Conditioning
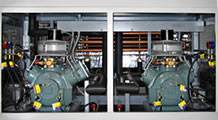
Chamber air in both the hot chamber(s) and the cold chamber is recirculated by high volume, stainless steel blowers drawing air in on the right side of the workspace and discharging on the left.
Air flows through a diffuser baffle to create a uniform high velocity environment in excess of 10 feet per second (600 feet per minute) around and through your test objects.
The air circulation blowers are driven by externally mounted TEFC (totally enclosed fan cooled) motors with dual ball bearing races, connected by large diameter extended stainless steel shafts. Fast-response open type heaters behind a radiation baffle raise chamber temperature in the hot compartment.
All electrical wiring meets the United States National Electric Code. UL and CSA approved components are used where possible.
Cooling
Mechanically refrigerated systems include a proportionally controlled cascade, two compressor, refrigeration system utilizing modern environmentally friendly refrigerants to cool the workspace in the cold compartment. The system includes automatic hot gas bypass and suction cooling unloading as well as Bemco’s exclusive, high performance coaxial cascade heat exchanger.
All systems are water cooled, have thermal and current sensors on each compressor, and feature numerous safety and reliability protection systems for dependable operation. Mechanical systems require no expendable refrigerants to recover to specified conditions.
For liquid nitrogen (LN2) cooled systems, chamber temperature is reduced by a proportionally controlled liquid nitrogen injection system utilizing both a control solenoid and a series mounted safety solenoid to positively interrupt nitrogen flow in the event of a malfunction. A relief valve and a line strainer are provided for dependable operation. A self-sealing vent system with an attachment coupling for remote piping by others, removes expanded nitrogen from the workspace.
Controls
Each Bemco FS2V chamber is furnished with a two channel microprocessor based programmable 1/4-DIN, solid state, 256-step ramping controller which includes a 4-line LCD interface display and a large red LED display. This instrument is pre-programmed to control both the hot chamber and the cold chamber automatically. Temperature inside both chambers is sensed in the return air (after the load) by precision thermocouples. An RS232 and RS485 interface is standard.
On the three zone chamber, an additional microprocessor based programmable 1/4-DIN, solid state, controller with a 4-line LCD interface display and a large red LED display is used to control the cold zone. This instrument is interlocked with the primary sequencing control, monitoring the two hot zones.
Heaters are wired in series with a separate heavy duty power contactor controlled by a factory preset high temperature safety control.
A microprocessor-based, FM Approved, high temperature safety control is standard on all hot chambers and a separate FM Approved low temperature control is standard on all liquid nitrogen cooled chambers.
Test Load Ratings
The ability of a Bemco FS2V or FS3V Thermal Shock Chamber to recover to the specified test temperature in the required time varies with the presentation of the test load to the circulating air in the chamber workspace.
Test load ratings also change with the Military Specification or test protocol, the test item density, and the test item’s material composition. A chart presenting properties of some common test load materials and simplified techniques for computing system performance is contained in the standard FS Series Technical Bulletin.
Test load arrangement and test fixturing can greatly affect the results you achieve by testing. The optimum thermal shock test fixturing pattern presents all sides of each test load to the flowing chamber air. Test fixturing that requires stacking parts or placing them in basket containers more than a few parts deep should be carefully analyzed for thermal response.
The analysis of the response of a specific combination of load, chamber, and specification can get quite complicated. Since we specialize in this type of work, we have automated programs that perform a very rigorous thermal analysis of both your test load and our thermal shock chambers.
We are happy to provide this service to you at no charge. For evaluation of component parts, at least two ounces (0.125 pounds) of representative parts of each type you want us to look at are required for analysis.
Optional Equipment
Both the FS2V and the FS3V systems are available in custom shapes and sizes. They are also offered with specially modified conditioning systems, air circulation patterns, transfer mechanisms, and control systems. Please request an analysis of your needs.
Available FS2V and FS3V Options include:
- Windows and interior lights in one or more compartments. Window sizes are 12” x 12” and 18” x 18” clear viewing area.
- A 1” traveling tube access port. This port exits through the chamber top and raises and lowers with the transfer cage.
- Access Ports in the side of any compartment. Standard sizes are 2”, 3”, 4” and 6.”
- Casters, four swivel type, with locks.
- Shelf pilasters and wire-type stainless steel shelves in each bay.
- Shelf pilasters and basket-type stainless steel shelves, 2” deep in each bay.
- LN2 boost cooling with vent for extra or back-up cooling on mechanically cooled systems.
- GN2 gas purge with pressure regulator, gauge, flow measuring and regulating valved rotameter, and vent in each bay.
- Desiccant drier purge with dual tower 10 cfm desiccant drier, pressure regulator, gauge, flow measuring and regulating valved rotameter, and vent, piped to each bay.
- For systems with mechanical refrigeration, two refrigeration gauges per compressor, four total, mounted in the refrigeration package available with or without isolation valves.
- A high capacity hydraulic transfer system for handling larger, overweight, loads.
- A heating system in the cold chamber to allow part-time use of the cold chamber as an environmental test chamber.
- An automatic cold chamber defrost system including a defrost heater and a defrost timer.
- A remote, air cooled, refrigeration system condenser for mounting by your qualified air conditioning contractor or Bemco factory technicians, up to 50 feet from the chamber, on a roof or outside your building.
- A quiet package to reduce noise on either liquid nitrogen or mechanically refrigerated systems.
Optional Instruments
Controls are mounted on the side to prevent dripping from damaging the instruments. Available instruments include:
- Microprocessor-based, FM Approved under-temperature safety control for a mechanically cooled FS2V or FS3V system. FM Approved over-temperature safety controls are standard on all systems and under-temperature controls are standard on LN2 cooled chambers.
- Remote control over an Ethernet Link.
- A 12 inch, chart printing, two or four channel circular chart recorder.
- A 4 channel strip chart recorder.
- A system elapsed time meter.
- A digital temperature indicator for FS2V, 2 Zone systems.
- A digital temperature indicator for FS3V, 3 Zone systems.
- A smoke alarm, one per bay, to monitor for problems with the test load.
- A 10 inch nominal, touch screen HMI, (Human Machine Interface) coupled to an Allen Bradley PLC to replace the main system controls and switches. This system includes a main switch and an emergency stop button.
Available Literature Includes:
Bemco FS and TS Series, Vertical and
Rotary Thermal Shock Chambers.
Twenty four standard models of vertical 2 and 3 Zone and twelve standard
models of rotary 2 Zone thermal shock chambers. Thermal shock heat
transfer and test load rating calculations are discussed. Document
is 12 pages, 766 KB download.
The systems described above are our Standard Models. We make custom equipment to your specifications. If you have any questions, need assistance in preparing a specification, or have a technical problem you want help with, we are ready. Our quotations and advice are free.